As the global beer market continues to grow, more and more entrepreneurs and investors are beginning to try to enter this industry which is full of business opportunities. As the core link of beer production, the construction and operation of a brewery directly affect production efficiency and the quality of the final product. As a modern business model, turnkey breweries have gradually become the preferred method chosen by many investors and entrepreneurs due to their efficiency, convenience, and professionalism. Simply put, a turnkey brewery means that customers only need to “take over the keys” and start production directly without undertaking complex construction, equipment procurement, installation, commissioning, and other tedious work. This guide will explore the concept of a turnkey brewery in detail, explain the brewing equipment required, and provide a comprehensive reference for those who are interested in investing or opening a brewery.
What is a turnkey brewery?
A turnkey brewery is a fully equipped brewing facility that can be put into production immediately after purchase. This means that the buyer does not have to go through the trouble of setting up each piece of equipment or process from scratch. Instead, everything from brewing pots, fermentation tanks, and cooling systems to other necessary tools is installed and put into use. A turnkey brewery is not a fixed template, but a complete set of equipment and services customized according to the needs and scale of the customer. These services include not only the configuration of brewing equipment but also plant construction, integration of automated control systems, optimization of production processes, personnel training, and after-sales services. In short, the turnkey model allows customers to avoid the tedious process of complex equipment procurement, plant construction, commissioning, and operation management and can focus on beer production and market operations.
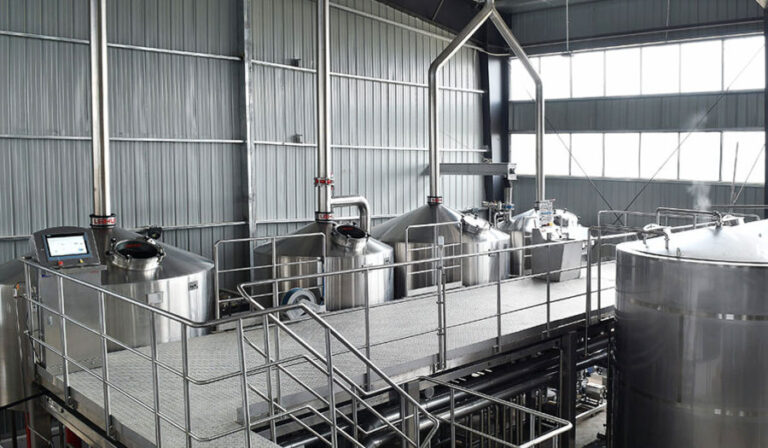
Brewing equipment required for a turnkey brewery
Malt crushing equipment
During the brewing process, the malt needs to be crushed first. Malt-crushing equipment usually includes a drum crusher or a hammer crusher. The crushed malt will enter the mash pot for subsequent processing.
Mash system
The mash system is the core of beer production. It is mainly responsible for converting starch in malt into sugar for yeast fermentation. The mash system includes a mash pot, a malt crusher, a filter, etc. The mash pot usually adopts an efficient heat exchanger design to ensure the efficiency and temperature control accuracy of the brewing process.
Boiling system
The boiling system is mainly used to boil the saccharified malt liquid and add hops to adjust the aroma and produce bitterness. During the boiling process, impurities will be removed, thereby improving the taste of the beer. The boiling pot is usually made of high-quality stainless steel to ensure food safety and corrosion resistance.
Fermentation tank
Fermentation is a key link in beer production. Yeast will convert sugar into alcohol during this process. The fermentation tank must have good sealing and temperature control functions to ensure that the yeast can ferment in an ideal environment. Modern fermentation tanks are usually equipped with temperature control systems, stirring systems and other equipment to ensure the uniformity and stability of the fermentation process.
Cooling system
During the brewing process of beer, especially after mash and boiling, it is necessary to cool down quickly to maintain the optimal fermentation temperature. The cooling system usually includes heat exchangers, cooling towers, condensers, etc., which can effectively reduce the temperature of the malt liquid and provide a suitable environment for subsequent fermentation.
Filtration system
During the fermentation and maturation process, beer will produce a large amount of solid impurities, which must be removed by the filtration system. Common filtration equipment includes plate and frame filters, centrifugal filters, etc. The filtered beer is clearer and has a smoother taste.
Packaging equipment
Packaging is the last link in beer production. Beer can be bottled, canned, or barreled, and the packaging equipment needs to be customized according to different packaging methods. Common packaging equipment includes bottling machines, canning machines, capping machines, labeling machines, etc.
Automated control system
Modern beer breweries are usually equipped with advanced automated control systems, which can monitor the entire production process in real-time through PLC (Programmable Logic Controller) and SCADA (Supervisory Control and Data Acquisition System). The automated control system can ensure accurate operation of each link, reduce manual intervention, and improve production efficiency.
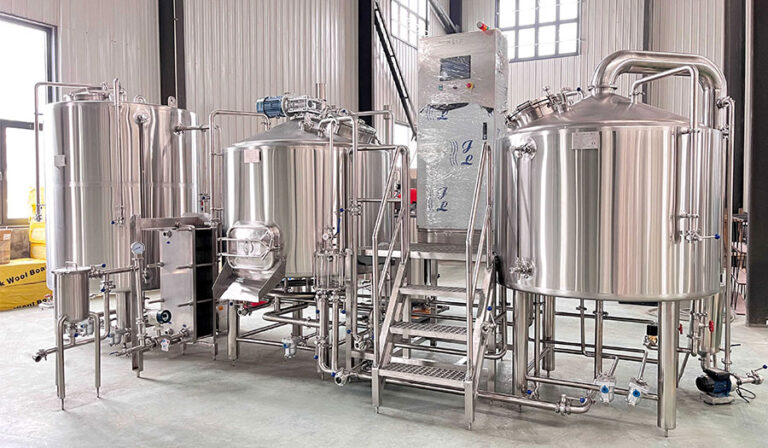
Turnkey Brewery Features
- Mashing: This is the first step where the crushed grains (mostly malted barley) are mixed with hot water in a mash-tun. The heat activates enzymes that convert the starches in the grains into fermentable sugars, creating a thick, porridge-like mixture called mash.
- Filtration: After mashing, the liquid is transferred to a container called a lauter tun. Here, the wort is separated from the liquid, which is now called wort.
- Boiling: The wort is then boiled in a brew kettle, which usually lasts about an hour. Hops are added at this point to add bitterness, flavor, and aroma to the beer. Boiling also sterilizes the wort, ensuring that no harmful microorganisms interfere with the fermentation process.
- Cooling: After boiling, it is critical to quickly cool the wort to a temperature suitable for yeast fermentation. Heat exchangers are often used to achieve this rapid cooling.
- Fermentation: The cooled wort is transferred to a fermenter and yeast is added. The yeast consumes the fermentable sugars in the wort, producing alcohol and carbon dioxide in the process.
- Packaging: Once fermentation is complete and the beer is mature, it is ready for packaging. Depending on the brewery’s capabilities, the beer can be packaged in bottles, cans, or kegs.
What are the types of turnkey breweries?
Nanobreweries
Nanobreweries are the smallest commercial breweries, with a production capacity of less than 3 barrels (about 300 liters). This type of brewery is ideal for entrepreneurs who want to develop their brewing hobby into a business, or businesses that want to provide specialty beers for their bars or restaurants. Due to their small production scale, nanobreweries can often innovate quickly and produce a wide variety of craft beers with unique flavors.
Microbreweries
Microbreweries have a production capacity of 3 to 15 barrels (about 300 to 1500 liters). This type of brewery has a larger production scale than nanobreweries, which can usually support local market distribution and meet the needs of a wider range of consumers. Small breweries can not only supply local bars, restaurants, and retailers but also have their bars or pubs provide products directly to consumers. Many microbreweries focus on producing specialty craft beers, with a wide range of products, from classic pale ales to experimental flavored beers. Due to their moderate scale, these breweries can ensure high product quality and have strong market adaptability.
Craft Breweries
Craft breweries are usually larger than microbreweries, with production capacities ranging from 15 to 60 barrels (about 1,500 to 6,000 liters). These breweries focus on handcrafted brewing, and their products are often known for their unique flavors and high quality. Compared with microbreweries, craft breweries usually have a wider distribution network, involving a wider range of regional distribution in addition to the local market, and may even enter the national market. Craft breweries have a variety of beers, and rich flavors, and usually focus on innovation and personalization, which attracts many beer lovers and followers of craft culture.
Industrial breweries
Industrial breweries are giants in the beer industry, with production capacities usually exceeding 60 barrels (6,000 liters), strong production capabilities, and a wide distribution network. These breweries are not only for local or regional markets, but their products often cover national and even international markets. Industrial breweries are large-scale, usually use efficient production lines and automation technology, and produce relatively standardized beer types to meet the needs of the mass market.
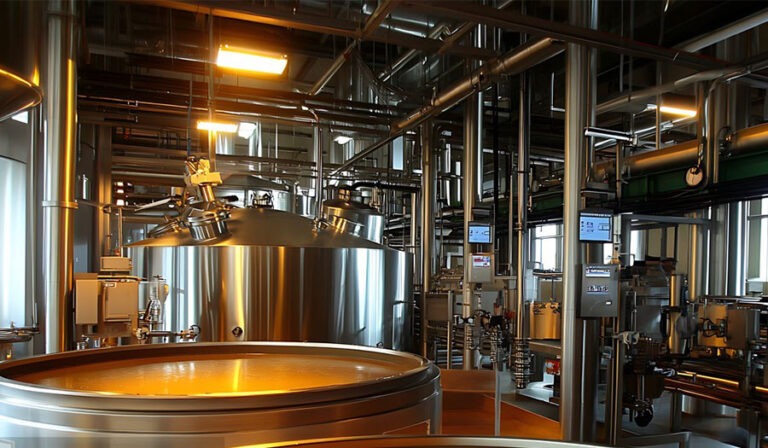
Advantages of turnkey breweries
Reduce the risk of plant construction
For most novice entrepreneurs or small businesses, building a brand new brewery means solving multiple links such as equipment procurement, construction, and commissioning. These links are prone to problems such as improper planning and improper equipment selection, resulting in waste of time and money, and even affecting production. Therefore, the turnkey brewery model can greatly reduce the complexity and risk of the project by providing a complete set of solutions.
Save time and energy.
In the traditional plant construction process, entrepreneurs need to carefully select brewing equipment, communicate with different suppliers, coordinate construction progress, etc. The whole process may take months or even years. After adopting the turnkey model, suppliers will provide one-stop solutions according to customer needs, reducing the coordination and work of multiple links. Customers only need to wait for delivery and put into production, which greatly saves time and energy.
Professional technical support
Turnkey brewery suppliers usually have rich industry experience and professional technical teams. They can not only provide customers with precise brewing equipment, but also provide optimization suggestions for production processes, technical training for equipment use, and later technical support. Customers do not need to worry about technical problems in equipment operation and can rely on the professional services of suppliers.
Efficient production and quality assurance
The design of turnkey breweries usually takes into full consideration the efficiency of the production process and the stability of product quality. Since the entire system is designed and integrated by a professional team, the efficiency and quality control of the production line are usually better than non-customized solutions. Customers can obtain more precise production processes and optimized processes to improve production efficiency and ensure the quality of beer.
Flexible customized solutions
Turnkey breweries are not limited to large-scale commercial production lines. For small and medium-sized manufacturers, suppliers can also provide customized solutions. Whether it is a small craft brewery or a large automated production line, suppliers can design and adjust according to customer needs to ensure that production needs of different scales and styles are met.
FAQ
What is the difference between a turnkey brewery and a traditional brewery?
The biggest difference between a turnkey brewery and a traditional brewery is the way the project is implemented. A turnkey brewery adopts a one-stop solution. The supplier is responsible for the entire process from design, equipment procurement to construction and installation. The customer can start production after receiving the “key”. Traditional brewery construction usually requires customers to participate in multiple links, such as selecting suppliers, negotiating equipment, supervising construction, etc. The process is cumbersome and time-consuming.
How long is the construction period of a turnkey brewery usually?
The construction period of a turnkey brewery generally depends on the scale and complexity of the project and the efficiency of the supplier. For small or medium-sized breweries, it usually takes 3 to 6 months to complete the design, equipment procurement, construction, and commissioning. Large or customized breweries may take longer, ranging from 6 months to a year.
Does the turnkey brewery include technical training?
Yes, most turnkey brewery suppliers will provide technical training services. The training usually includes operating equipment, commissioning production lines, production process management, quality control, and health and safety.
Can turnkey breweries be customized?
Yes, turnkey breweries can be customized according to customer needs. Whether it is a small craft brewery or a large-scale industrial brewery, customers can customize corresponding solutions according to production capacity, equipment configuration, production process, and other requirements. Customized services can help customers better adapt to market demand and brand positioning.