With the continuous advancement of science and technology, the application of automation technology in various industries is becoming increasingly popular, and the beer manufacturing industry is no exception. The automation system of the brewery not only improves production efficiency, optimizes product quality, reduces production costs, and ensures production safety. The automated brewing system has become a core component of modern breweries. It replaces traditional manual operations through intelligent control systems, thereby achieving precise control of the production process, real-time data monitoring, and remote management of equipment.
What is a brewery automation system?
The brewery automation system consists of a series of interconnected hardware and software. It monitors and controls all stages of beer production in real-time through highly integrated automation technology. These stages include raw material processing, brewing, fermentation, packaging, and other process automation systems. The goal is to achieve precise control, improve production efficiency, reduce labor costs, improve product quality, and minimize human errors.
The automated brewing system mainly achieves comprehensive control of the beer production process through integrated control systems (such as PLC, DCS, etc.), technology, data acquisition and analysis systems, and real-time monitoring platforms. Through the high integration and customization of equipment, breweries can achieve the following core goals:
- Improve production efficiency: The automation system can accurately control the production process and reduce production stoppages and waste caused by human errors.
- Optimize product quality: The precise control of automation equipment keeps the taste, flavor, aroma, and other indicators of each batch of beer consistent.
- Energy saving and consumption reduction: Automation technology helps to optimize energy utilization, reduce energy consumption in the production process, and reduce unnecessary waste of resources.
- Ensure food safety: The automation system ensures that the production process meets food safety standards through real-time monitoring, data recording, and traceability.
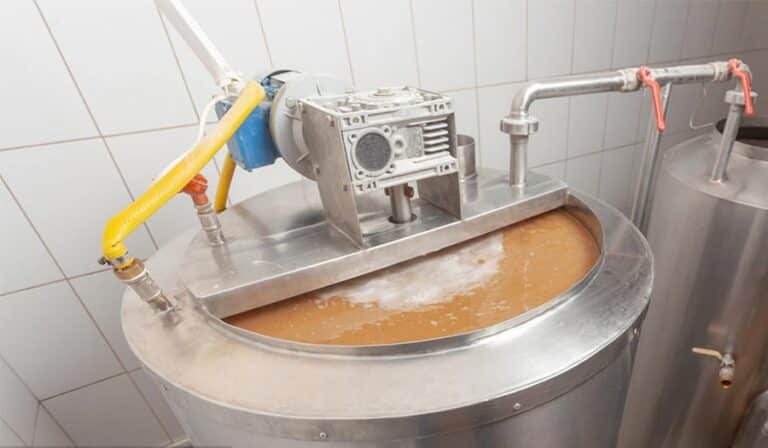
The main equipment of the automated brewing system
Raw material handling system
Processing is the first step in beer brewing, including the preparation of malt, hops, water, and beer. The automated raw material handling system monitors the delivery, mixing, and piping process of raw materials through precision raw material equipment and sensors. The system includes the following main components:
- Malt crusher: crushes malt particles into suitable particles to facilitate the extraction of sugar. The automated control system can adjust the working parameters of the equipment according to the requirements of the crushing particle size.
- Automated batching system: used to accurately control the ratio of different raw materials. The system automatically measures, pipes, and mixes raw materials according to the set formula and production batch.
- Water treatment equipment: ensure that the water quality meets the requirements of beer production. The automated water treatment system includes water quality monitoring, filtration, softening, and disinfection equipment, and monitors the water quality in real-time through sensors to ensure the stability of water quality during the brewing process.
Sistema de fabrico de cerveja
Brewing is the core link of beer production, involving multiple processes such as mash, boiling, and cooling. The sistema de fabricação de cerveja automatizado ensures that every step of the brewing process is carried out under the best conditions by precisely controlling parameters such as temperature, time, and pressure. The main equipment includes:
- Mash Tun: used to mix malt with water and convert starch into sugar through the heating process. The mashpot is usually equipped with a temperature control system, a stirring system, and a liquid level monitoring system to ensure the efficient mash
- Brew Kettle: During this process, hops are added and boiled to extract aroma and bitterness. The automation system controls the boiling temperature, time, and amount of hops added to ensure the consistency of flavor.
- Heat exchanger: used to quickly cool the boiled wort to the fermentation temperature. The automation system ensures the efficiency and stability of the cooling process and avoids the impact of temperature fluctuations on fermentation.
Sistema de fermentação
Fermentation is one of the most critical stages in beer brewing, which converts sugar into alcohol and fermentation. The automated fermentation system ensures the stability of the fermentation process by accurately controlling factors such as temperature, pressure, and pH. The main equipment includes:
- Fermentation tank: It is the main container for fermentation, usually equipped with automation equipment such as temperature control, pressure sensor, and liquid level monitoring to achieve precise environmental control.
- CO2 recovery system: By capturing the high CO2 generated during the fermentation process, it is recovered and used in other production stages. The automated CO2 recovery system can be used to monitor the generation and recovery efficiency of high CO2 in real-time.
- Automated dissolved oxygen system: During the fermentation process, the oxygen content has an important influence on the activity of yeast. The automated dissolved oxygen system monitors the dissolved oxygen content in real-time through sensors and adjusts the gas supply to ensure the smooth progress of fermentation.
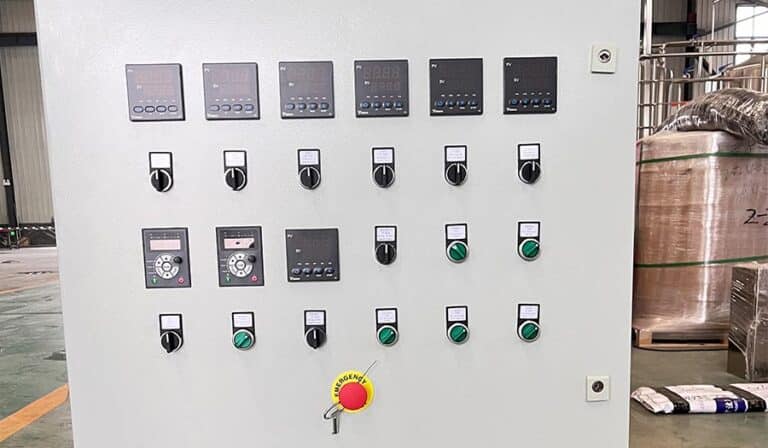
Warehousing and logistics system
Beer after fermentation usually needs to be filtered and packaged. The automated filtration system can effectively improve the suspended matter, yeast, etc. in the beer to ensure the clarity and stability of the beer. The automated packaging system ensures that the filling volume, number of bottles, cap seam, label printing, etc. of each bottle of beer meet the standards. The main equipment includes:
- Filtration system: including filter presses, centrifuges, etc., used to improve the accuracy of beer. The automated system ensures the filtration effect by monitoring the filtration speed, filtration pressure, and quality of the beer.
- Filling line: Automated filling uses precise filling machines to ensure the accurate capacity of each bottle of beer and avoid waste. The filling system needs to be equipped with sensors to detect in real-time whether the bottle mouth is clean and the bottle cap is tight.
- Packaging and packaging line: Automated packaging equipment ensures that the packaging, labeling, and packing processes of beer bottles are efficient and fast. This system is usually linked with the logistics management system to realize the automated management of inventory.
Filtration and packaging system
Through automated conveyor belts, stackers, and filling dock management systems, breweries can realize automated warehousing, storage, and outbound operations.
Brewing process with automated systems
- Mashing: Grains are soaked in hot water to convert starches into fermentable sugars. Automated systems maintain precise temperatures to ensure optimal enzyme activity. With programmable steps, you can easily manage temperature rests for complex beers such as lagers or wheat beers.
- Filtration: After mashing, wort (the sugary liquid) is separated from the grains. Automated systems use pumps and valves for filtration, providing a constant flow rate to avoid clogging and ensure maximum sugar extraction.
- Boiling: During the boiling process, hops are added to the wort to add bitterness and flavor. Automatic boil kettles allow you to set the amount of hops to be added at a specific time, ensuring a consistent taste.
- Cooling: Cooling the wort quickly is essential to prevent contamination and prepare for fermentation. Advanced chillers in automated systems make this process fast and efficient.
- Fermentation: Fermentation takes place in temperature-controlled fermenters. Automated equipment monitors temperature, pressure, and CO2 levels to optimize yeast performance and beer quality.
- Packaging: Some automated systems also assist with kegging or bottling, providing an end-to-end brewing solution.
Types of automated brewing systems
Home brewing system
Home brewing is becoming more and more popular, and with it has come the emergence of user-friendly automated systems designed for home use. These systems often strike a balance between automation and manual control, allowing hobbyists to fine-tune the brewing process while still enjoying the convenience of automation. Features often include automatic temperature control, programmable brewing schedules, and integrated cleaning systems. Home systems are typically compact and designed to fit into a standard kitchen, making them ideal for beginners or those with limited space.
Commercial brewing system
For those looking to brew beer on a large scale, commercial automation systems offer significant upgrades in capacity and functionality. These systems are designed for microbreweries or small craft breweries that need to produce consistent, high-quality beer in large quantities. Commercial systems often include advanced features such as multi-stage mashing, automated grain handling, and sophisticated monitoring software. These systems require more space and a higher initial investment but are more scalable and efficient.
Industrial-grade brewing system
Industrial-grade sistemas automatizados de fabricação de cerveja are top-of-the-line systems used by large breweries to produce large quantities of beer with precision. These systems are fully automated, with every aspect of the brewing process—from raw material handling to packaging—controlled by advanced software and robots. Industrial systems are designed to achieve maximum efficiency, reduce labor costs, and minimize the possibility of human error. They are also highly customizable, allowing breweries to quickly adapt to changing market demands.
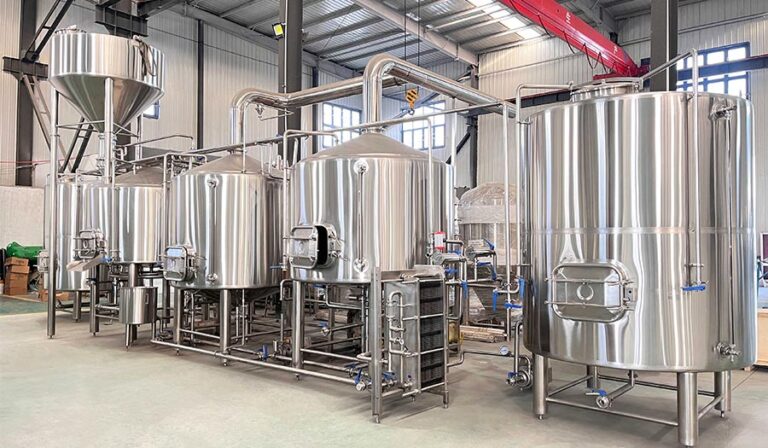
Control and monitoring of automation systems
The automation systems of modern breweries usually adopt integrated control and monitoring systems. These systems are based on efficient industrial control computers, combined with PLC, DCS (distributed control system), SCADA (data acquisition and monitoring control system), and other technologies to form an efficient and reliable production control platform. Through the collaborative work of these systems, breweries can achieve full-process monitoring, precise regulation, and efficient management, which not only improves production efficiency but also ensures the stability of beer quality.
- PLC system: used to control various mechanical equipment in the production process, such as pumps, valves, conveyor belts, etc. Through the PLC system, operators can control and monitor production equipment in real-time to ensure accurate execution of each link.
- DCS system: used for complex process control, such as precise adjustment of parameter processes such as temperature, pressure, flow, etc. The DCS system can provide multi-point control and full-process monitoring to ensure the stability of the production process.
- SCADA system: provides real-time monitoring and data recording of process production. The SCADA system can not only display production parameters in real-time but also help factories optimize processes through data analysis.
Pros and Cons of Automated Brewing Systems
Advantages of Automated Brewing Systems
One of the biggest advantages of automated brewing systems is the ability to produce consistent beer batch after batch. Automation minimizes the risk of human error, which is essential to maintaining the quality and flavor of beer. These systems also save time and energy, allowing brewers to focus on other businesses or hobbies. In addition, automation can increase efficiency, reduce waste, and potentially reduce production costs over time.
Disadvantages of Automated Brewing Systems
On the downside, automated brewing systems can be expensive, especially for advanced commercial and industrial equipment. The initial investment can be a barrier for small breweries or homebrewers. Additionally, while automation reduces the need for human intervention, it also requires a certain level of technical expertise to effectively operate and maintain the system. Finally, some brewers feel that automation takes away the hands-on, manual aspect of brewing, which for many can be an essential part of the craft.
Conclusão
The rise of automated brewing systems has revolutionized the art of beer brewing, making it easy, efficient, and exciting. Whether you’re a hobbyist dreaming of brewing the perfect IPA beer or a commercial brewer scaling up production, these systems offer unparalleled control and consistency. The breweries of the future will not only rely on traditional automation equipment, but will combine advanced predictive analysis technology, automated robotics technology, and intelligent and IoT logistics management systems to achieve more efficient production modes.