V moderní průmyslové výrobě jsou míchací nádrže důležitým typem zařízení a jsou široce používány v mnoha průmyslových odvětvích, zejména v chemickém, potravinářském, farmaceutickém, nátěrovém a každodenním chemickém průmyslu. Jejich hlavní funkcí je míchat různé materiály v určitém poměru a určitým způsobem, aby se dosáhlo jednotnosti a stability výrobku. Se zrychlujícím se procesem industrializace se technologie míchacích nádrží neustále vyvíjela. Od původního jednoduchého mechanického míchání až po současnou integrovanou regulaci teploty, tlaku, automatizaci a další funkce se stala nepostradatelným výrobním nástrojem ve všech oblastech života.
A míchací nádrž (míchačka nebo míchací nádrž) je zařízení používané k míchání, rozpouštění, disperzi nebo homogenizaci dvou nebo více materiálů. Obvykle se skládá z nádoby, míchacího zařízení a pohonného zařízení. Míchací nádrže se široce používají v mnoha průmyslových odvětvích, jako jsou chemický, potravinářský, farmaceutický průmysl, výroba denních chemikálií, nátěrových hmot a ochrana životního prostředí. Používají se k účinnému míchání surovin v různých formách (pevných, kapalných, plynných) v určitém poměru, určitým způsobem a podle určitých požadavků, aby se zajistilo, že směs bude mít jednotné složení a stabilní vlastnosti.
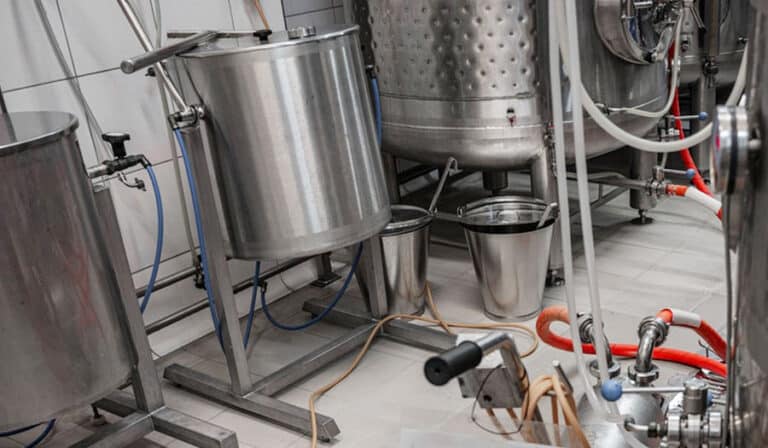
Význam mísicích nádrží
- Udržujte konzistenci: Jedním z hlavních důvodů, proč se v každém odvětví používá míchací nádrž, je zajištění jednotnosti a kvality konečného produktu. V průmyslových odvětvích, jako jsou farmaceutický průmysl, potravinářství, výroba nápojů a chemikálií, je přesné míchání složek velmi důležité. Pomocí míchací nádrže mohou společnosti dosáhnout rovnoměrného míchání a zajistit tak stálou kvalitu a účinnost každé šarže výrobků.
- Zvýšení efektivity výroby: Míchací nádrže výrazně zvyšují efektivitu výroby tím, že zjednodušují a urychlují proces míchání. V minulosti mohlo být míchání velkého množství materiálů ručně nebo pomocí základního vybavení časově náročné a pracné. Míchací nádrže vybavené pokročilou technologií míchání dokáží rychle a efektivně zpracovat velké množství složek.
- Efektivní integrace komponent: Další klíčovou úlohou mísicích nádrží je integrace různých složek do jednoho celistvého produktu. To je důležité zejména v průmyslových odvětvích, kde může být kombinace různých látek náročná. Například v chemickém průmyslu vyžadují některé reakce přesné podmínky, jako jsou specifické teploty nebo tlaky, a směšovací nádrže mohou tyto podmínky zajistit.
- Flexibilita výroby: Míchací nádrže nabízejí vynikající flexibilitu a jsou vhodné pro výrobu široké škály produktů. Tato flexibilita je obzvláště cenná pro průmyslová odvětví, která potřebují přecházet mezi různými recepturami nebo postupy bez rozsáhlých prostojů. Rozpouštění a dispergace: Míchací nádrž dokáže účinně rozpouštět nerozpustné látky do roztoku nebo dispergovat pevné částice do kapaliny a vytvořit tak rovnoměrný roztok nebo suspenzi. Typickými aplikacemi mísicích nádrží jsou například emulgace, dispergace, rozpouštění a další procesy. Například při výrobě emulzí, nátěrů, čisticích prostředků a dalších produktů jsou zapotřebí míchací nádrže.
- Regulace teploty a tlaku: Mnoho výrobních procesů vyžaduje reakce nebo míchání za specifických teplotních a tlakových podmínek. Míchací nádrže jsou obvykle vybaveny zařízeními pro regulaci teploty, tlaku a ohřevu/chlazení, aby se udržela stabilita reakčního prostředí a zajistila přesná kontrola reakčního procesu, a tím se zlepšila kvalita výrobku.
- Podporovat reakci nebo syntézu látek: V některých chemických a farmaceutických výrobních procesech plní míchací nádrže nejen úlohu míchání materiálů, ale také podporují reakci nebo syntézu surovin řízením podmínek, jako je míchání, teplota a tlak, čímž vznikají požadované produkty.
V jakých odvětvích se používají míchací nádrže? Chemický průmysl
Chemický průmysl
Chemický průmysl je jedním z průmyslových odvětví, kde se míchací nádrže používají nejčastěji. Výroba chemických produktů obvykle zahrnuje míchání různých chemických surovin, které mají často velké rozdíly ve fyzikálních a chemických vlastnostech, jako je hustota, viskozita, rozpustnost atd., takže požadavky na míchací zařízení jsou velmi vysoké.
- Míchání chemických reakcí: V procesu chemické reakce je často nutné přesně smíchat různé reaktanty v určitém poměru a nechat je reagovat za vhodných podmínek. Například při výrobě syntetických pryskyřic, plastových přísad nebo hnojiv mohou míchací nádrže zajistit stabilní podmínky míchání, aby se zajistila úplná reakce surovin a zlepšila kvalita a výstup výrobků.
- Rozpouštění a disperze: Mnoho surovin v chemickém průmyslu je třeba rozpustit nebo dispergovat v míchacích nádržích. Například při výrobě nátěrových hmot je třeba dosáhnout promíchání pigmentů a pryskyřic pomocí účinného míchacího zařízení. Míchací nádrže mohou zajistit rovnoměrnost roztoku a zabránit stratifikaci a srážení.
- Reakce při vysoké teplotě a vysokém tlaku: Při některých chemických reakcích musí suroviny reagovat při vyšších teplotách nebo tlacích, což vyžaduje, aby směšovací nádrž měla vlastnosti odolnosti vůči vysokým teplotám a vysokým tlakům a byla schopna stabilně pracovat v extrémních podmínkách.
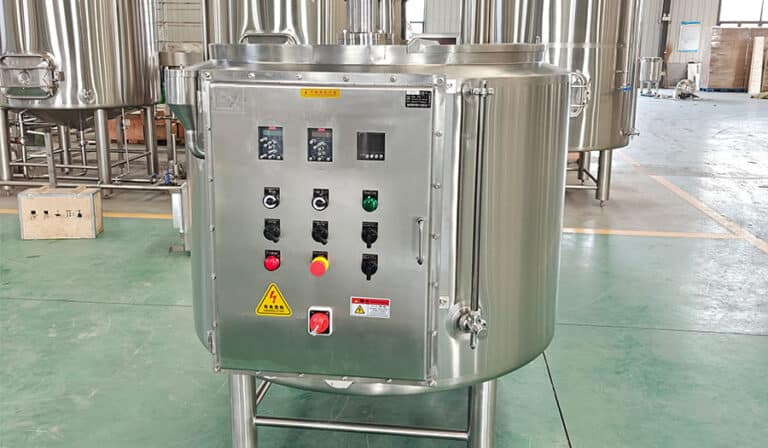
Potravinářský průmysl
V potravinářském průmyslu se také hojně používají míchací nádrže. Zpracování potravin obvykle vyžaduje přesné míchání surovin, aby byla zajištěna chuť, nutriční hodnota a stabilita výrobku.
- Míchání kapalin a prášků: Mnoho potravinářských výrobních procesů vyžaduje míchání kapalných a práškových surovin. Například při přípravě nápojů, šťáv, mléčných výrobků a koření mohou míchací nádrže zajistit rovnoměrné rozložení různých složek a zabránit jejich rozvrstvení nebo vysrážení.
- Výroba omáček a koření: Při výrobě koření, jako je sójová omáčka, omáčky, kečup atd., je třeba v míchacích nádržích přesně dávkovat a míchat různé složky. Takové míchací nádrže jsou obvykle vybaveny systémy regulace teploty, aby byla zajištěna stabilita a chuť koření.
- Míchání těsta a potravinářských přísad: V procesu výroby potravin, jako je chléb a sušenky, hrají důležitou roli také míchací nádrže. Jejím hlavním úkolem je rovnoměrně promíchat suroviny, jako je mouka, cukr, sůl a olej, aby se zlepšila struktura těsta a v konečném důsledku se zlepšila chuť a kvalita potravin.
- Homogenizace při zpracování potravin: Některé špičkové potraviny, jako jsou mléčné výrobky, zmrzlina atd., je třeba homogenizovat, aby se zajistila chuť a jemnost výrobku. V míchacích nádržích lze jemným mícháním a kontrolou dosáhnout dobré homogenity a zabránit rozvrstvení surovin.
Farmaceutický průmysl
Farmaceutický průmysl má na míchací nádrže mimořádně vysoké požadavky, protože přímo ovlivňují účinnost a bezpečnost léčiv. Ve farmaceutickém procesu je třeba míchat různé suroviny podle přísných požadavků na poměr, aby byla zajištěna konzistence kvality a stabilita léčiv.
- Míchání pevných léčiv: Mnoho léků existuje ve formě prášku nebo granulí. Během výrobního procesu se k rovnoměrnému promíchání různých surovin používají míchací nádrže, aby se zajistila konzistence účinných látek v každé dávce. To je nezbytné pro výrobu pevných léčiv, jako jsou tablety a tobolky.
- Míchání a příprava tekutých léčiv: Některé léky musí být v tekuté formě, např. injekce, perorální tekutiny atd. Ve výrobním procesu takových přípravků hrají klíčovou roli míchací nádrže. Mohou zajistit rovnoměrné míchání surovin, zabránit vysrážení nebo rozvrstvení léčiv a dosáhnout přesné kontroly koncentrace.
- Příprava pastovitých léčiv: Výroba léků, jako jsou náplasti a krémy, je rovněž závislá na podpoře míchacích nádrží. Míchacími nádržemi lze nejen dosáhnout účinného míchání, ale také zajistit stabilitu pasty a zabránit oddělování složek.
- Kontrola kvality léčiv: Farmaceutický průmysl má velmi přísné požadavky na kvalitu výrobků. Míchací nádrže jsou obvykle vybaveny mnoha funkcemi, jako je regulace teploty, regulace tlaku, regulace otáček atd., které zajišťují, že proces míchání probíhá za specifických podmínek tak, aby byly splněny přísné normy kvality.
Denní chemický průmysl
Míchací nádrže v každodenním chemickém průmyslu jsou také široce používány. Výrobní proces chemických výrobků denní potřeby, jako je šampon, sprchový gel, kosmetika atd., vyžaduje přesné míchání více složek, aby byla zajištěna kvalita a účinek výrobků.
- Emulgace a dispergace: Mnoho chemických výrobků denní potřeby, jako jsou pleťové vody, krémy, přípravky pro péči o pleť atd., se obvykle skládá z oleje, vody a emulgátorů. Míchací nádrž dokáže tyto složky rovnoměrně promíchat a vytvořit stabilní emulzi nebo pastu díky účinné technologii emulgace a dispergace.
- Míchání příchutí a základních materiálů: Při výrobě parfémů a vonných produktů jsou požadavky na míchání aromat a základních materiálů velmi vysoké. Míchací nádrž může účinně upravit poměr aromat a základních materiálů, aby byla zajištěna stabilita parfémů a stálost vůně.
- Příprava čisticích prostředků: Výroba každodenních chemických produktů, jako jsou prací a čisticí prostředky, je rovněž neoddělitelně spojena se směšovacími nádržemi. Míchací nádrž zajišťuje rovnoměrné rozložení různých povrchově aktivních látek, rozpouštědel a přísad, což zajišťuje, že čisticí prostředek má dobrý čisticí účinek.
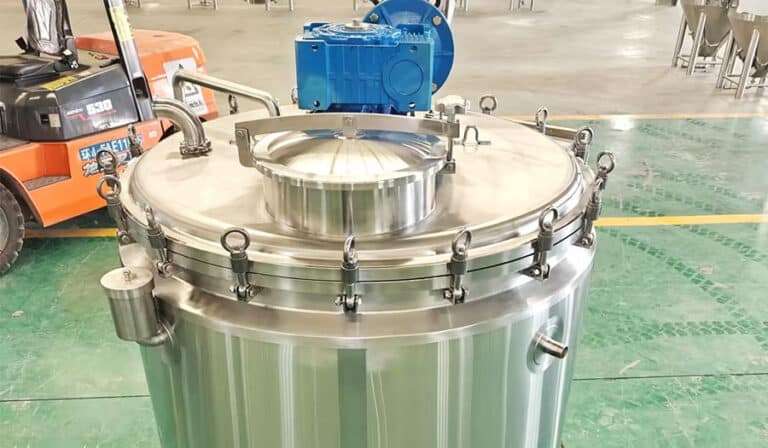
Výhody směšovacích nádrží
- Účinné míchání: Míchací nádrž dokáže rychle a rovnoměrně promíchat různé látky díky účinnému míchacímu zařízení, což výrazně zvyšuje efektivitu výroby. Tradiční metody míchání mohou trvat dlouho, ale moderní míchací nádrže díky pokročilé konstrukci mohou dokončit účinné míchání v kratším čase a ušetřit výrobní náklady.
- Přesné ovládání: Moderní míchací nádrže jsou obvykle vybaveny automatickými řídicími systémy, které mohou v reálném čase monitorovat a upravovat rychlost míchání, teplotu, tlak a další parametry, aby bylo zajištěno, že proces míchání splňuje předem stanovené požadavky. Tato přesná kontrola může výrazně zlepšit konzistenci a stabilitu výrobku a snížit odchylky a chyby ve výrobním procesu.
- Lze je přizpůsobit různým materiálům: Míchací nádrž si poradí s různými materiály, jako jsou kapaliny, pevné látky, plyny, a dokonce i viskózní nebo vysoce viskózní materiály. Je velmi přizpůsobivá a podle výrobních potřeb lze zvolit různé typy míchacích nádrží, které si poradí s různými materiály a výrobními podmínkami.
- Úspora energie a snížení spotřeby: Spotřebu energie a ztráty materiálu lze snížit vhodně navrženými míchacími nádržemi. Například optimalizací způsobu míchání a zlepšením účinnosti výměny tepla lze snížit energetické ztráty a zlepšit míru využití energie při výrobě. Míchací nádrž může zároveň snížit plýtvání surovinami, protože dokáže zajistit plné využití materiálů.
- Zlepšení kvality výrobků: Přesným řízením procesu míchání může míchací nádrž zajistit rovnoměrnost a stabilitu konečného výrobku, a tím zlepšit jeho kvalitu. V potravinářském, farmaceutickém, kosmetickém a dalších odvětvích může rovnoměrné míchání nejen zlepšit vzhled, chuť a funkci výrobku, ale také prodloužit jeho trvanlivost.
- Snížení nákladů na práci a materiál: Většina moderních míchacích nádrží je vybavena automatickými řídicími systémy, které mohou výrazně snížit manuální zásahy, náklady na pracovní sílu a chyby ve výrobních operacích. Zároveň díky efektivnímu způsobu práce může zlepšit celkovou efektivitu výrobní linky a ušetřit náklady na materiál.
- Vysoká bezpečnost: Mnohé konstrukce míchacích nádrží zohledňují bezpečnostní aspekty výrobního procesu, jako je míchání materiálů s vysokou teplotou, vysokým tlakem nebo hořlavých a výbušných materiálů. Moderní míchací nádrže jsou obvykle vybaveny několika bezpečnostními ochrannými zařízeními, jako je automatické uvolnění při příliš vysokém tlaku, automatické chlazení při příliš vysoké teplotě atd. pro zajištění bezpečnosti během výrobního procesu.
- Snadno se čistí a udržuje: Moderní míchací nádrže jsou obvykle vyrobeny ze snadno čistitelných materiálů odolných proti korozi, jako je nerezová ocel, a mají odnímatelnou a omyvatelnou konstrukci pro snadné čištění a údržbu. To je důležité zejména pro odvětví s vysokými hygienickými požadavky, jako jsou potravinářství a farmaceutický průmysl, aby se zabránilo křížové kontaminaci materiálů a zajistilo se, že výrobky splňují hygienické normy.
Souhrn
Jako vysoce účinné průmyslové zařízení je míchací nádrž široce používána v různých průmyslových odvětvích, zejména v chemickém, potravinářském, farmaceutickém, nátěrovém a každodenním chemickém průmyslu, kde hraje zásadní roli. Dokáže dosáhnout rovnoměrného míchání, rozpouštění, dispergace, reakce a dalších procesních požadavků různých materiálů prostřednictvím přesného míchání, regulace teploty a tlaku, čímž zvyšuje efektivitu výroby, zajišťuje kvalitu výrobků a snižuje výrobní náklady.