Getting your beer into bottles shouldn’t be the hardest part of brewing. But many small breweries and beverage startups struggle with inconsistent fill levels, contamination, and inefficient manual bottling. That’s where a high-quality beer bottle filling machine changes everything.
Beer bottle filling machines help craft breweries and beverage producers efficiently and hygienically package carbonated beverages in bottles or cans. They ensure consistent fill levels, support various bottle sizes, and are available in automatic, semi-automatic, or manual models to meet production needs from startup to commercial scale.
What is a Beer Bottle Filling Machine?
A beer bottle filling machine is specialized bottling equipment designed to accurately fill carbonated or non-carbonated beverages—like beer, cider, or kombucha—into bottles or cans. These machines range from compact manual fillers for startups to advanced semi-automatic or automatic beer bottling machines used in commercial breweries.
The main purpose of these machines is to maintain the beer’s carbonation, hygiene, and shelf life by controlling oxygen exposure, fill level, and capping. They often include integrated counter-pressure filling systems and are compatible with glass bottles, aluminium cans, and PET bottles.
How Does a Beer Bottle Filling Machine Work?
The filling process typically involves the following steps:
Rinsing bottles to eliminate dust or microbes.
CO2 purging to reduce oxidation in carbonated beverages.
Counter-pressure filling or gravity filling depending on the model.
Level adjustment and foam control.
Capping or crowning using an integrated capper.
Labeling and packing if part of a bottling line.
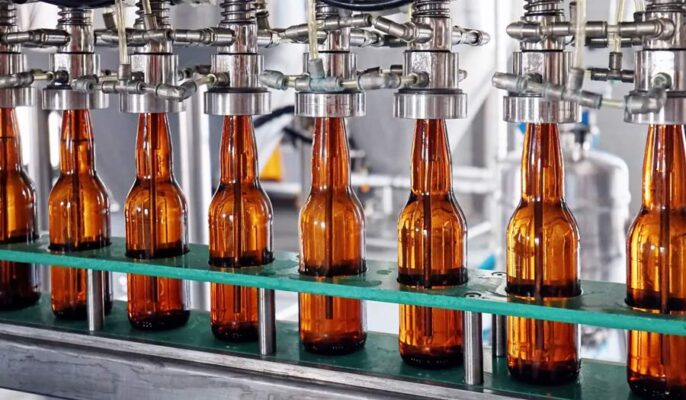
What Types of Bottle Filling Machines Are Available?
There are several categories of beer filling machines designed for different production volumes and business types.
Type | Best For | Capacity |
---|---|---|
Manual Bottle Filler | Home brewers, test runs | 50–100 bottles/h |
Semi-Automatic Filler | Small breweries | 200–600 bottles/h |
Automatic Bottle Filler | Commercial-scale production | 1,000+ bottles/h |
Some brands also offer monoblock systems that integrate rinsing, filling, and capping into one streamlined unit, ideal for breweries looking to save space and labor.
Why Is Counter Pressure Filling Important?
Counter pressure filling is essential for bottling carbonated beverages. It prevents excess foaming and carbonation loss by equalizing pressure inside the bottle and the filling tank. This technique helps maintain the beer’s CO2 level, reduces oxygen pickup, and prevents overfilling.
This makes counter pressure bottle filling machines the go-to solution for bottling craft beer, carbonated soft drinks, and even distilled spirits like cider and kombucha with light carbonation.
What Bottle Sizes and Types Are Supported?
Modern bottle fillers support a variety of formats:
Standard 12 oz or 330ml beer bottles
22 oz or 750ml swing-top bottles
Glass bottles with crown or screw caps
Cans from 250ml to 500ml
PET bottles with special capping options
Advanced systems can be adjusted to handle different bottle sizes without major setup changes, offering great flexibility for seasonal brews or private label packaging.
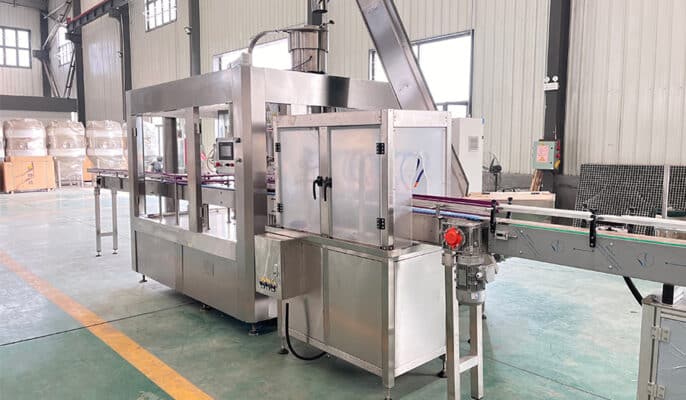
Manual, Semi-Automatic, or Automatic: Which One to Choose?
Manual fillers are best suited for hobbyists or entry-level production. Semi-automatic fillers add consistency and speed while still requiring some operator intervention. Automatic bottling machines streamline every step—rinsing, filling, capping, and labeling—with minimal labor.
Choosing the right model depends on your budget, scale, labor availability, and long-term brewing goals. For example:
A semi-automatic beer bottling machine offers a great ROI for startups.
An automatic beer canning line is ideal for mid-sized breweries with distribution plans.
What Materials Should You Look for in a Bottle Filling Machine?
Durability and hygiene matter. Most reliable bottling machines use food-grade stainless steel (304 or 316) for all parts in contact with liquid. This ensures:
Easy to clean surfaces
Resistance to acids and sanitizers
No contamination from rust or leaching
Also consider whether the model supports CIP (Clean-in-Place) systems for faster sanitation cycles, especially if you’re bottling kombucha, cider, or other sugar-rich beverages.
What Additional Equipment Complements a Beer Bottle Filler?
To build an efficient beer bottling line, you’ll likely need:
Rinse and sanitize stations
CO2 purging devices
Capper (for crown caps, swing-tops, screw lids)
Labeling machine
Conveyor system
Keg or brite tank as the liquid source
Having a full bottling line reduces downtime and boosts consistency across your entire packaging process.
Can This Equipment Be Used for Other Beverages?
Absolutely. Besides beer, these machines can also bottle:
Sparkling water
Hard cider
Kombucha
Distilled spirits
Carbonated beverages like soft drinks
Just ensure the machine can handle the specific carbonation levels, liquid viscosity, and bottle pressure rating required for your product.
How Much Does a Beer Bottle Filling Machine Cost?
Pricing depends on speed, automation level, and accessories:
Machine Type | Estimated Price Range |
---|---|
Manual Bottle Filler | $500 – $2,000 |
Semi-Automatic Filler | $3,000 – $10,000 |
Automatic Bottling Line | $15,000 – $100,000+ |
Factors influencing cost:
Brand reputation
Included accessories (capper, conveyor)
Customization and support
Type of bottles and caps supported
As a brewing equipment manufacturer, we offer flexible custom solutions with full technical support and international shipping.
What Are the Core Types of Beer Bottle Filling Machines?
Beer bottle filling machines come in various configurations tailored to specific scales and production goals. Understanding these types helps brewers choose the most efficient solution for their operations. Among the most common are manual, semi-automatic, and automatic machines.
Manual fillers are ideal for startups or small-scale brewers, offering cost savings and basic functionality. Semi-automatic machines strike a balance between automation and hands-on control, often featuring a bottle rinser, filler, and capper in one compact design. Automatic systems, on the other hand, are geared toward commercial production, capable of handling thousands of bottles per hour with minimal human intervention.
Counter pressure filling technology, present in many automatic and semi-automatic machines, helps reduce foam and preserve carbonation during the fill process. This is especially important for carbonated beverages like beer, cider, or kombucha.
What Is the Difference Between Bottling and Canning for Beer?
Both bottling and canning are popular beer packaging formats, but each comes with unique benefits. Bottling is a traditional choice, especially for craft beers and premium lines. Glass bottles offer superior oxygen protection and are often preferred for their aesthetic appeal and recyclability.
Canning, however, has surged in popularity in recent years. It is more lightweight, offers better light protection, and is easier to store and ship. Modern canning machines can fill and seam hundreds of aluminum cans per minute, making them highly efficient for large-scale operations.
While bottles may require a capper and possibly a labeler, cans typically need a seamer, CO2 purge system, and liquid filler optimized for their format.
The choice between the two often depends on your market, branding goals, and available space. Some brewers even opt to install both canning and bottling lines to increase flexibility.
How Do Counter Pressure Bottle Fillers Work?
Counter pressure fillers are a staple in modern craft beer packaging, especially for carbonated beverages. The process involves pressurizing the bottle with CO2 before filling to minimize foam and oxidation. This method preserves the carbonation level and ensures a consistent fill level.
Once the bottle is pressurized, the valve opens, allowing beer to flow into the bottle at a controlled rate. Some systems feature an adjustable fill level, allowing brewers to customize the process based on bottle size or style.
This technique is crucial for high-carbonation beers and small-scale operations where minimizing product loss is key. A counter pressure bottle filler can be a worthwhile investment for any serious craft brewery.
What Key Features Should You Look For in a Bottle Filling Machine?
When evaluating beer bottle filling machines, several technical and performance factors should be considered:
Speed and throughput: Measured in bottles per minute (BPM)
Automation level: Manual, semi-automatic, or fully automatic
CO2 purging: Helps extend shelf life and maintain carbonation
Capper compatibility: Crown caps, twist caps, or flip-top
Material quality: Food-grade stainless steel construction for durability and hygiene
Fill accuracy and level control: Prevents waste and ensures label compliance
For expanding breweries, scalability and modular upgrades can future-proof the investment. Machines that integrate rinsing, filling, and capping in one monoblock unit are especially valued in space-limited facilities.
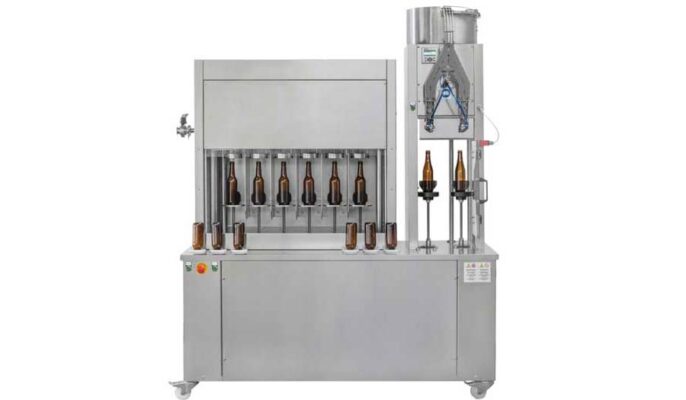
How to Integrate a Bottle Filler into Your Existing Brewery?
Integrating a bottle filler into your current brewhouse or packaging system requires careful planning. Begin by evaluating your production volume and packaging goals. Layout and footprint are critical — ensure there’s space for conveyors, rinse units, and cappers.
Utility requirements, such as power, water supply, CO2, and compressed air, must also be assessed. If you’re upgrading from manual to semi-automatic or automatic systems, staff training and SOP adjustments are essential for a smooth transition.
Many commercial fillers come with plug-and-play designs and technical support to streamline integration. Look for suppliers that offer floor planning assistance, custom configurations, and post-installation maintenance services.
What Role Does a Capper Play in the Bottling Line?
A capper is critical in ensuring that every filled bottle is securely sealed to preserve freshness, carbonation, and flavor. Whether your beer bottle uses crown caps, twist caps, or flip tops, the capper ensures a consistent seal that prevents leaks and oxidation.
Cappers can be manual, semi-automatic, or integrated into a monoblock automatic bottling system. Commercial systems often combine the capper with the filler to reduce footprint and improve efficiency. For carbonated beverages, cappers also work in sync with counter pressure fillers to minimize gas loss.
How Can Automation Improve Beer Bottle Filling Efficiency?
Automation significantly improves efficiency, throughput, and consistency in beer bottle filling. Fully automatic systems can fill, cap, and label thousands of bottles per hour, often requiring minimal operator oversight.
Automated systems come with programmable touchscreen interfaces, adjustable settings for different bottle sizes, and self-cleaning functions. This reduces downtime and operator error. Breweries scaling from craft to commercial operations will benefit from faster production cycles and lower cost-per-unit over time.
FAQs
What is the most common size for beer bottles in filling machines?
Standard bottle sizes include 330ml, 500ml, and 750ml. Machines are often adjustable to accommodate a range of bottle sizes.
Can I use the same filling machine for beer and kombucha?
Yes. As long as the machine supports carbonated beverages and proper sanitization, it can handle both.
Is it worth investing in semi-automatic beer bottling machines?
Absolutely. They provide an ideal balance of affordability, precision, and scalability, especially for growing breweries.
What’s the typical lead time for installing a new bottle filling machine?
Lead times vary, but average around 4 to 8 weeks, including customization, manufacturing, and shipment.
Are your filling machines suitable for export?
Yes. Our beer bottle filling machines comply with international standards and include technical support, remote guidance, and localized configurations.
Conclusion: Why Choose Our Beer Bottle Filling Machines?
At our brewery equipment manufacturing facility, we combine engineering expertise with real-world brewing experience to deliver equipment that meets global demands. From small batch craft beer to full-scale production, our beer bottle filling machines are:
Built from 304 stainless steel for durability and hygiene
Equipped with counter pressure filling and precise level control
Designed with both starter brewers and large breweries in mind
Supported by a global network of distributors and technical experts
Explore our beer bottling solutions and take the next step in scaling your brewing business.